청결도: 베어링 장착 과정과 관련된 모든 표면을 완벽한 표준에 따라 철저하게 청소합니다. 업계 표준 세척제 및 방법을 활용하여 가장 잘 지워지지 않는 오염 물질도 제거할 수 있습니다. 깨끗한 상태를 유지하려면 용제 세척, 초음파 세척, 증기 탈지 등의 방법을 사용하십시오. 장착 표면이 깨끗하면 조기 마모나 손상을 일으킬 수 있는 연마 입자나 잔해물이 베어링 어셈블리에 들어갈 위험이 최소화됩니다.
구성 요소 검사: 베어링 설치와 관련된 모든 구성 요소를 꼼꼼하게 검사합니다. 확대 도구와 염료 침투 검사, 자분 탐상 검사 등의 비파괴 검사 기술을 활용하여 아주 작은 표면 결함이나 이상 현상도 감지할 수 있습니다. 베어링 궤도, 롤링 요소 및 케이지 구조와 같은 중요한 영역에 세심한 주의를 기울이십시오. 베어링 어셈블리의 무결성과 신뢰성을 보장하기 위해 마모, 구멍, 균열 또는 부식의 징후가 있으면 즉시 교체해야 합니다.
적절한 취급: 전체 설치 과정에서 최대한 주의하고 정밀하게 베어링을 취급하십시오. 클린룸 프로토콜을 사용하거나 보풀이 없는 장갑을 착용하여 피부 기름이나 먼지 입자로 인한 오염을 방지하십시오. 베어링 리프터, 진공 흡입 장치 또는 자석 핸들러와 같은 특수 취급 장비를 활용하여 운송 및 설치 중 물리적 손상 위험을 최소화하십시오. 베어링 부품 내에 미세 구조 변화나 응력 집중을 초래할 수 있는 갑작스러운 충격, 낙하 또는 충격을 피하십시오.
정렬: 업계 표준을 초과하는 정확도로 정밀한 샤프트 및 하우징 정렬을 달성합니다. 레이저 간섭계 또는 컴퓨터 정렬 시스템과 같은 고급 정렬 기술을 사용하여 미크론 미만 수준의 정렬 공차를 달성합니다. 베어링 배열의 장기적인 안정성에 영향을 미칠 수 있는 작동 하중, 열팽창 효과 및 동적 힘을 설명하기 위해 동적 정렬 분석을 수행합니다. 베어링 성능을 손상시킬 수 있는 오정렬로 인한 응력이나 왜곡을 완화하기 위해 심 조정, 열 보상 또는 굴곡 분석과 같은 수정 조치를 구현합니다.
윤활: 가장 까다로운 작동 조건에서 베어링 성능을 최적화하는 정밀도 수준의 윤활유를 도포합니다. 유체역학적 윤활 분석이나 경계막 모델링과 같은 고급 윤활 기술을 활용하여 가장 적합한 윤활제 유형, 점도 및 적용 방법을 결정합니다. 자동화된 윤활 시스템 또는 중앙 집중식 윤활 장치를 구현하여 베어링 어셈블리 전체에 일관된 윤활유 공급 및 분배를 보장합니다. 실시간 상태 모니터링 시스템 또는 윤활유 분석 기술을 사용하여 윤활유 품질 및 상태를 모니터링하여 잠재적인 오염, 성능 저하 또는 윤활 특성 손실을 감지합니다.
온도 제어: 베어링 설치 과정 전반에 걸쳐 엄격한 온도 제어 조치를 유지하여 베어링 무결성을 손상시킬 수 있는 열 변형, 치수 변화 또는 야금학적 변경을 방지합니다. 유도 히터, 저항 히터 또는 액체 질소 침지 수조와 같은 정밀 가열 또는 냉각 시스템을 구현하여 균일한 온도 프로파일을 달성하고 열 구배를 최소화합니다. 열전대, 적외선 센서 또는 열화상 카메라를 사용하여 실시간으로 온도 변동을 모니터링하여 가열, 냉각 및 설치 후 안정화 단계에서 지정된 온도 제한을 준수하는지 확인합니다.
쌍을 이루는 단열 테이퍼 롤러 베어링
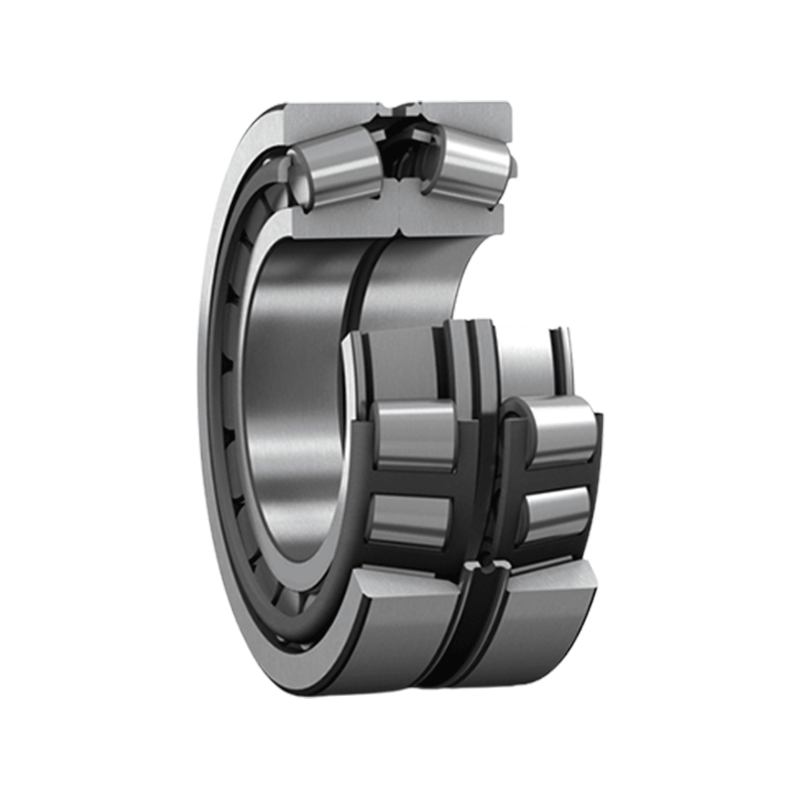